Many of us focus on plantation drives and opt for environment-friendly products to reduce carbon emissions. But in the process, we tend to overlook, or are unaware altogether, that the very walls surrounding us in our homes are also massive contributors to climate change.
Carbon-negative
This means removing CO₂ from the atmosphere or sequestering more CO₂ than is emitted. This might include a bioenergy process with carbon capture and storage.
CO₂: problem or opportunity?
Global progress on emissions reduction has been so slow that simply cutting emissions won’t avert a climate catastrophe. Even if the world manages to achieve net-zero emissions by 2050, we may still blow our “carbon budget” – the amount of CO₂ that can be emitted if Earth’s temperature rise is to stay below 1.5℃ this century. So we must find ways to first eliminate emissions, then remove existing CO₂. It is foreseeable Earth will one day rely on carbon-negative technologies that draw CO₂ from the air and stabilise it in useful products. For example, direct air carbon capture and storage (which is still under development) could one day remove CO₂ and use it in products such as building materials and plastics.
The problem becomes evident if we understand the process of making cement.
What is cement?
Cement is used in construction to bind other materials together. It is mixed with sand, gravel and water to produce concrete, the most widely used construction material in the world. Over 10bn tonnes of concrete are used each year.
The industry standard is a type called Portland cement. This was invented in the early 1800s and named after a building stone widely used in England at the time. It is used in 98% of concrete globally today, with 4bn tonnes produced each year.
Why does cement emit so much CO2?
Around half of the emissions from cement are process emissions arising from the reaction above. This is a principal reason cement emissions are often considered difficult to cut: since this CO2 is released by a chemical reaction, it can not be eliminated by changing fuel or increasing efficiency.
A further 40% of cement emissions come from burning fossil fuels to heat kilns to the high temperatures needed for this calcination process. The last 10% of emissions come from fuels needed to mine and transport the raw materials.
Efficiency gains alone will, therefore, not be enough to significantly cut the sector’s emissions.
Have cement emissions been reduced?
The average CO2 intensity of cement production – the emissions per tonne of output – has fallen by 18% globally over the past few decades, according to Chatham House. However, the sector’s emissions as a whole have risen significantly, with demand tripling since 1990.
Progress so far has come in three main areas. First, more efficient cement kilns have made production less energy-intensive. This can improve further: global average energy use per tonne of cement is still around 20% higher than products with the current best available technology and practice.
Second, the use of alternative fuels has also lowered emissions – for example, using biomass or waste in place of coal. This is especially the case in Europe, where around 43% of fuel consumption now comes from alternatives, Chatham House says.
Third, reducing the proportion of Portland clinker in cement has also cut emissions. “High-blend” types of cement can reduce emissions per kilogram by up to four times, according to Chatham House. Clinker can be substituted with other cement-like materials, including waste from coal combustion and steelmaking. This can affect the cement’s properties, however, so is only suitable for some end uses.
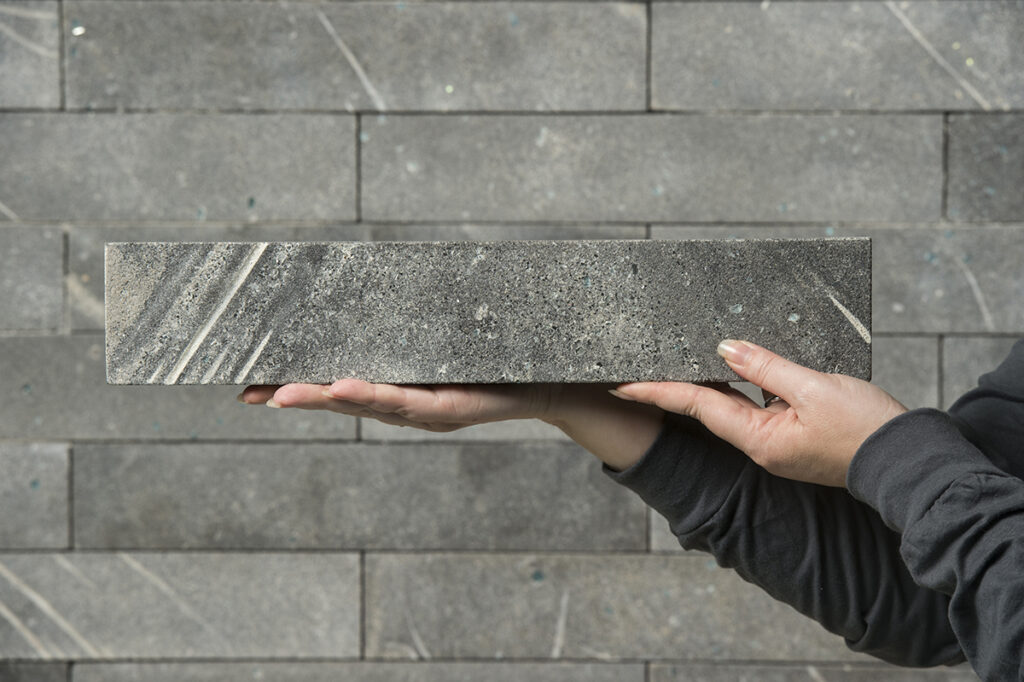
Raw material such as limestone and clay comes from quarries. The materials are crushed and mixed with iron ore or ash and fed to cylindrical kilns at around 1,450 degrees Celsius. The process is called calcination, which splits the mixture into calcium oxide and CO2, giving out a new product called clinker. The new marbled-sized and grey product is cooled and mixed with gypsum and limestone and sent as a ready-mix to concrete companies.
Half of the CO2 emissions from cement happen during the process. If cement were considered a country, it would become the third-largest CO2 emitter in the world, surpassing a massive country like India.
But a Roorkee and Visakhapatnam based social enterprise, GreenJams, might just have an alternative. The venture is creating carbon-negative building material from agriculture biomass and hemp blocks.
We often overlook the perspective of carbon emissions by cement materials in the construction industry. Several types of bricks have been invented by researchers for the betterment of the environment. Among such, one stands out as the Carbon-Negative Brick that cuts carbon emissions as well as construction cost by 50%. It is also known as Carbon Busters or Carbon Eating Bricks or Carbon Negative Bricks, and many more.
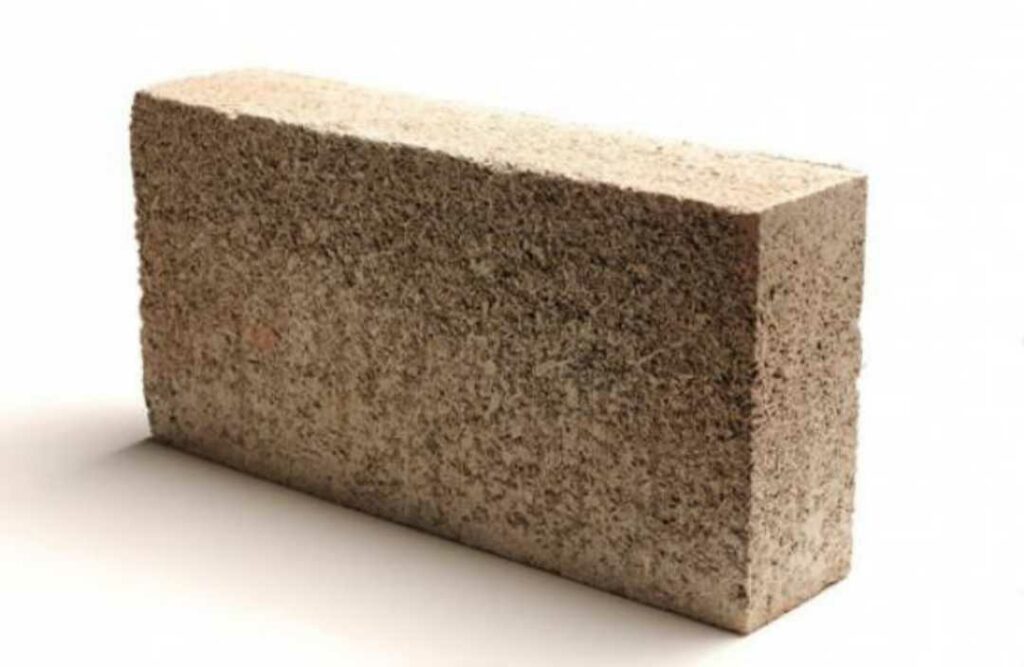
Properties of Carbon Negative Brick
- t is built by using over 50% recycled aggregate. This implies that the raw materials are not newly produced, and hence it saves the environment.
- The brick has the same strength as a traditional red brick fresh from the kiln, but it has less water absorption propensity, more excellent thermal conductivity, catches tonnes of CO2, and has a life span of at least 75 years.
- The density of cement brick is 1440 kg/m3, and that of carbon eating brick is 1200 kg/m3. This implies that the brick is less dense and hence has less weight.
- These bricks are 30% lighter than conventional bricks, which makes it easier for workers for transportation.
- Such bricks have a smooth surface compared to conventional bricks, making it easier to apply primer, paints, and plastering.
- Residential house construction can be completed in a few days with these bricks compared to conventional bricks that take months for completion due to various factors.
- Such bricks trap about 31 pounds of carbon dioxide instead of emitting it into the atmosphere.
- It takes 24 hours to cure such bricks and can store up to three kilos of CO2.
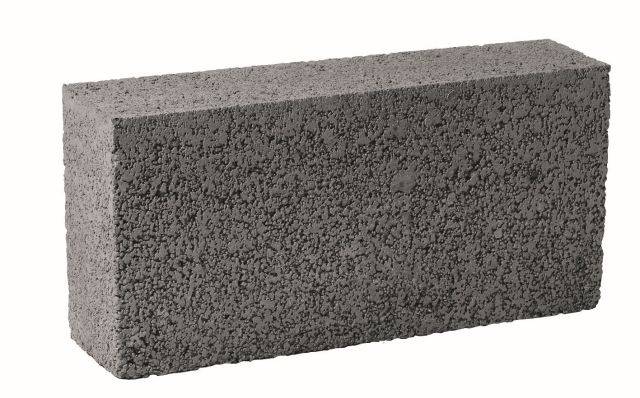
Conclusion
These carbon-negative blocks are essential to our environment as they reduce pollution to a greater level. The greenhouse gases are contributed mainly by carbon dioxide, which is immensely released by the cement industry. Hence, it is crucial to produce more eco-friendly blocks that are environmentally friendly and have compressive strength and other features similar to conventional bricks.
Sources; The better India
Tags: environment-friendly products, climate change, emissions, bioenergy process, carbon-negative technologies.